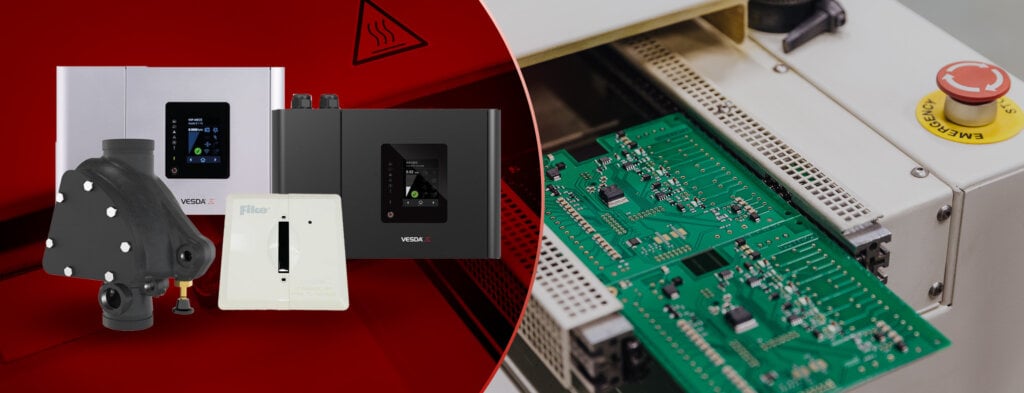
Table of Contents
Introduction
Semiconductor facilities can cost billions of dollars just as an initial investment. This means you should protect your business with the most accurate and efficient fire safety technology currently available. Fire Protection in these facilities is essential because they have fabrication areas and cleanrooms, which closely involve the use of hazardous production materials (HPMs) in daily processes. These HPMs range from metals and alloys to solvents and chemicals. Consequently, you must ensure protection in every stage of production, including cleanroom production, storage and transportation of the hazardous materials. Due to the toxic or flammable nature of the materials used in fabrication areas, the NFPA, OSHA, and the IBC have strict standards that must also be met in these facilities. In this blog, we will discuss those requirements and how you can protect your high-value goods and machinery in fabrication areas.
What Is a Cleanroom?
At the center of the semiconductor manufacturing process is the cleanroom. According to ISO 14644, a cleanroom is classified as “a room in which the concentration of airborne particles is controlled, and which is constructed and used in a manner to minimize the introduction, generation, and retention of particles inside the room.” To be more specific, the cleanroom is essential to a semiconductor facility because all fabrication takes place there. By the same token, airborne particles are extremely detrimental to chip production, and may cause defects in the microstructures of the semiconductor. As a prevention measure, cleanrooms must maintain tight control over variables such as temperature, humidity, airflow, noise, lighting, vibration, and particles. Regulating these variables is essential to prevent damage to structures as small as 30 nanometers produced by photolithography.
Due to the nature of cleanrooms, a single fire can contaminate the entire cleanroom, damage your products, incur costly damages, and cause delays in production. This factor is significant because once a cleanroom has been contaminated, it is no longer meets ISO standards, and all operations must halt. Even more, ionic contaminants can lead to corrosion on the metallic surfaces of equipment in the cleanroom. Consequently, these factors make fire safety even more important in these facilities. Rapid fire detection and suppression can minimize damages and lower the time it takes to decontaminate following the event. More importantly, it can be the difference between losing machinery of costs upwards of millions of dollars and quickly resuming production.
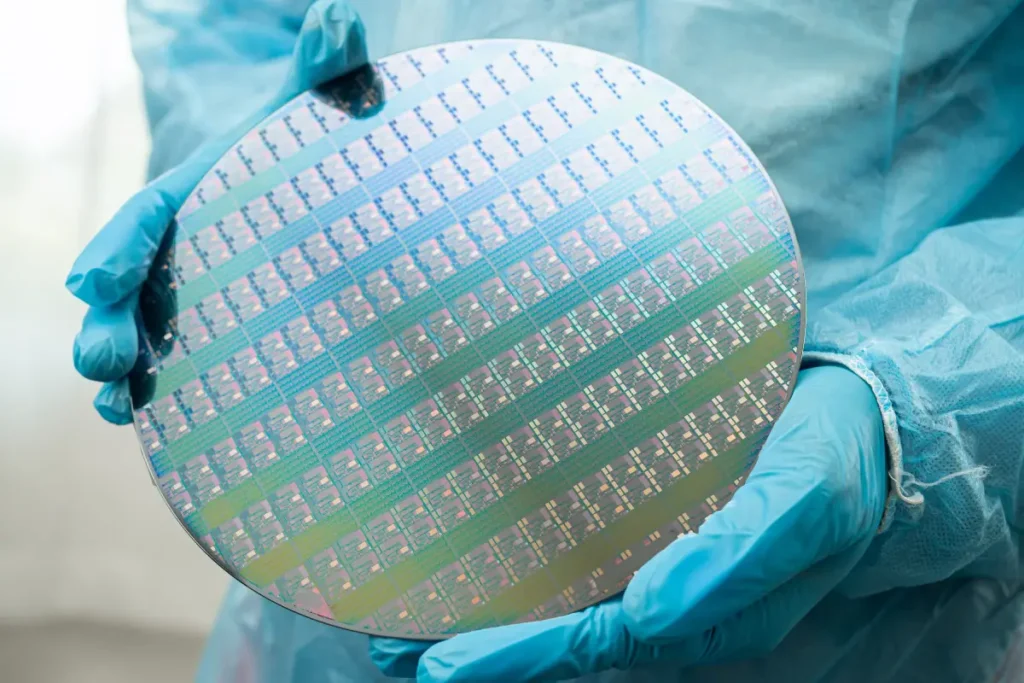
Worker holding a silicon wafer for semiconductor manufacturing
What Is the NFPA 318 Standard for Semiconductor Facilities
The standard that governs fabrication areas is NFPA 318, Standard for the Protection of Semiconductor Fabrication Facilities. In fabrication areas, you require an automatic fire suppression system. Fire suppression will reduce the spread of fire when flammable materials (gases, liquids, or dusts) are present. The suppression system design must align with NFPA guidelines, and may incorporate clean agent, C02, or sprinkler systems.
Automatic sprinkler systems are a vital component of fire safety in semiconductor fabrication facilities. They are required anywhere there is a high risk for fire, and they are necessary to protect paths of egress. Sprinklers are required to protect gas cabinets, exhausted enclosures, service corridors, production workstations, storage rooms, nonmetallic exhaust ducts, and fabrication rooms. To add, these sprinklers should be electrically supervised and provided with alarms, so further actions may be taken for the emergency.
This leads another vital fire safety measure that is required by national standards—alarm system supervision. According to NFPA codes, you are required to have an emergency control station that provides 24/7 monitoring of your fire alarm system. Monitoring is essential to ensure that the right person is notified when an abnormal situation occurs. Afterwards, they can determine the next steps to handle the situation and mitigate any damages and setbacks.
IBC and OSHA Fire Codes
Fabrication areas also require proper ventilation and fume hoods over certain production areas. These fume hoods prevent the buildup of toxic or flammable gases, which could present safety and fire hazards. These systems should be designed in accordance with NFPA 69 and NFPA 70 for class I, Division 2 hazardous locations. Thus, electrical equipment and devices within 5 feet of workstations in which flammable or pyrophoric gases or flammable liquids should also have adequate exhaust ventilation. With the increasing prevalence of pyrophoric materials in manufacturing, flame detection is essential in protecting your premises and workers.
Effective Fire Prevention Measures
Cleanrooms contain expensive and high-purity equipment, including steppers and scanners for photolithography, etching, cleaning, and doping. Moreover, expensive equipment like integrated circuits are manufactured in these rooms, where layers are formed on the circuits over many weeks. And so, a ruined production run can be costly, ruining entire batches of chips at one time. Thus, it is imperative to have an effective fire suppression system to mitigate damage and facilitate quick cleanup.
Fire suppression measures include sprinkler systems, clean agent systems, and inert gas systems. You will want to reduce the contamination of your cleanroom and damage to precious goods as much as possible, so a clean agent or inert gas system is recommended. These systems will leave the least amount of residue, and don’t have to be cleaned extensively after a fire event. Additionally, CO2 or fine water mist systems are ideal for risks related to flammable liquids or chemicals while minimizing damage to electrical equipment.
Smoke Detection in Fabrication Areas
Cleanrooms are similar to data centers because their systems use large amounts of electricity in a space with high airflow. In cleanrooms, HEPA filters are used alongside high air change rates to reduce the amount of particles in the air. However, due to the high airflow, spot smoke detection may be delayed or disrupted. A better alternative for this occupancy lies in aspirating smoke detection. Detectors like those from the VESDA-E series can draw in air through sampling tubes for fast and accurate smoke detection. Even more, aspirating smoke detectors are not affected by the high airflow spaces in cleanrooms and fabrication spaces. VESDA systems are also effective for protecting under floor void and sub-fab areas, which are used to house cable trays and support equipment for the cleanroom. Offering very early smoke detection, VESDA systems are proven to be effective for semiconductor and integrated circuits manufacturing.
Keep Reading: Emergency Power Shutdown Controls >>
Conclusion
Adhering to NFPA standards is essential for safeguarding both personnel and assets. Key fire protection measures include automatic suppression systems, flame and smoke detection technologies, and proper measures to mitigate risks from flammable materials.. By implementing these critical fire safety practices, facilities can minimize damage, reduce downtime, and preserve what is important to your business.
Ultimately, a proactive approach to fire safety—incorporating proper system design, regular maintenance, and staff training—is essential to minimize the risk of fire and ensure that your facility is prepared for emergencies. By adhering to fire safety codes and regulations, you create a safer, more resilient environment for staff. At FireAlarm.com, our expert team is ready to assist you with system design, installation, inspection, and maintenance services tailored to your needs. Reach out to us today to discuss how we can get your business compliant with the codes.
Related Products
$2,663.00
$8,635.00
$5,371.00
$3,984.00
$1,567.00
$2,881.00
$376.99
$2,650.00