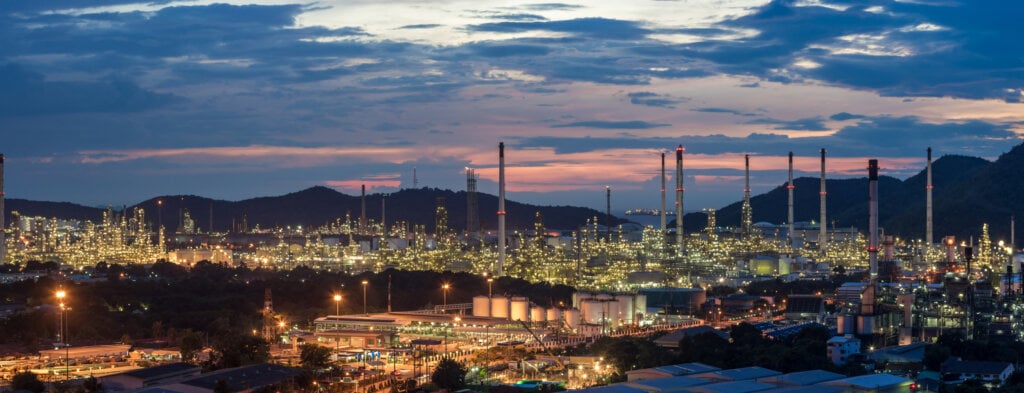
Table of Contents
Introduction
The NFPA separates different fire hazard or explosive occupancies using Classes and Divisions. This system classifies your facility based on what dangers could be present. It further subdivides these classes into divisions based on the frequency the flammable material is present and the manner in which they are handled. If you are in an occupancy that handles flammable materials, it is important to know these classifications so you can remain up to code.
Hazardous Area Classification Chart
This chart maps the groupings used by the NFPA to classify hazardous areas. Every hazardous site will have one class and one division. For example, a mining site may be considered class II, division 1, since there might be charcoal or other explosive dusts that are consistently exposed in the atmosphere.
Classes
- Class I
- Gases or liquids in quantities sufficient to product explosive or ignitable mixtures.
- Examples: formaldehyde, hydrogen, ethanol, ammonia
- Gases or liquids in quantities sufficient to product explosive or ignitable mixtures.
- Class II
- Combustible dusts that have a risk of causing a fire or explosion.
- Examples: Metal dusts, charcoal, wood dusts
- Combustible dusts that have a risk of causing a fire or explosion.
- Class III
- Ignitable fibers or flyings
- Examples: Cotton, rayon, cocoa fiber
- Ignitable fibers or flyings
Divisions
- Division 1
- An ignitable concentration of gases, vapors, dusts, or combustible materials are consistently present under normal operating conditions
- Division 2
- A closed system normally confines all combustible materials; however, these materials may escape under abnormal or fault conditions of the system or ventilation equipment
Groups for Hazardous Materials
Gases falling under Class I categories, identified as groups A through D, exhibit varying explosive potentials. Among these, group A gases, exemplified by acetylene, produce the most formidable explosive pressures, while group D gases, like propane, yield the least. Manufacturing equipment for group A settings poses the greatest challenge due to the heightened explosive energy involved.
Groups E, F, and G fall under class II, and these groups contain hazardous dusts. Group E refers to atmospheres with combustible or conductive metal dusts. Group F contains carbonaceous dusts, while group G contains non-conductive, combustible dusts, like wood and plastic.
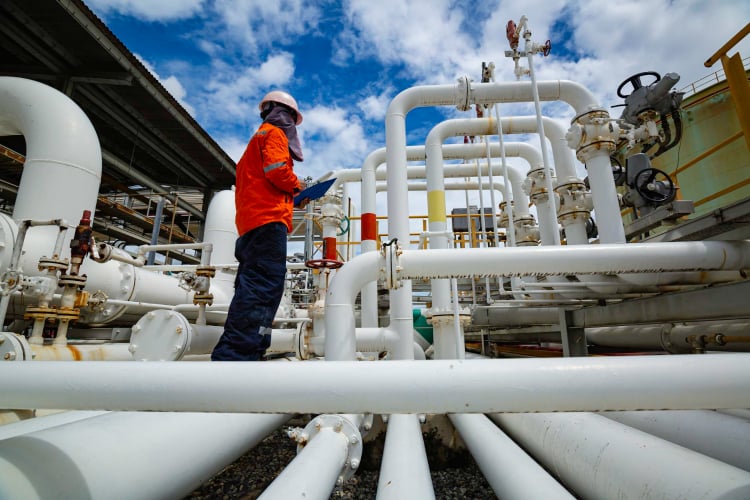
Conventional Practices In Hazardous Locations
Identify Fire Risk
Common events that may occur due to flammable materials include fire, flash fire, deflagration, and explosions. For this reason, you may require explosion-proof or intrinsically safe tools and machines. To guarantee the safety of your personnel, ensure that your devices meet the fire standards set by the NFPA 70 and NFPA 72. Moreover, confirm that these devices are endorsed by trusted 3rd party certification organizations like Factory Mutual (FM) or Underwriter Laboratories (UL).
If you are in a facility that handles combustible dusts, you should perform a dust hazards analysis (DHA) to determine the full extent of the dangers to your workers and goods. Furthermore, you are also required to have a DHA reviewed and updated every 5 years, as per the NFPA 72 (40.5.1.4). Moreover, you should also have a fire hazard analysis, based on your occupancy type. To ensure your protection, make sure the analysis is conducted by a reliable fire protection engineer (FPE). Based on this analysis, you can determine the location and spacing of your detectors.
Keep Reading: Introducing Fike Small Space Suppression Systems >>
Gas Detection
If you have a facility that handles flammable or toxic gases, including gas detectors should be your top priority. Gas detection can provide an early warning of gas leaks, and a general sense of its location; gas detection helps occupants to evacuate before a fire disaster occurs, and it helps you to locate the source of the problem. Furthermore, a common practice is combining line detection with point detectors for the most economical and effective coverage. It is not uncommon for point detectors to be placed in high-risk areas, while line detectors are placed at the boundaries of the facility, where they can track the movement of gas between different areas.
There are several technologies available to detect the presence of dangerous gases. Gas detection is available through catalytic detectors, electrochemical detectors, toxic gas detectors, and combustible gas detectors. To add, there is infrared detection, which senses gas along a path, and acoustic detection, which relies on noise patterns.
Fire Detection
While gas detection is useful for identifying risk, you should still implement detection measures that indicate that a fire has actually started. Both smoke and flame detection are a part of a complete fire safety strategy in a hazardous area. With smoke detectors, there are both photoelectric and ionization technologies available. Meanwhile, flame detectors can sense the particles emitted by all flames directly within their line of sight using various technologies. There is a wide spectrum of flame detection technologies, including ultraviolet, infrared, ultraviolet/infrared, and multi-spectrum infrared detection.
Conclusion
Authentication by a professional engineer is essential to determine the necessity of specialized equipment in an area. You should approach this decision with caution and in cooperation with your local authority having jurisdiction. If you need a professional to determine your fire protection needs, don’t look any further than FireAlarm.com’s system design services! Our team is equipped with the knowledge and experience to consult you on any fire system application and cater to your needs.